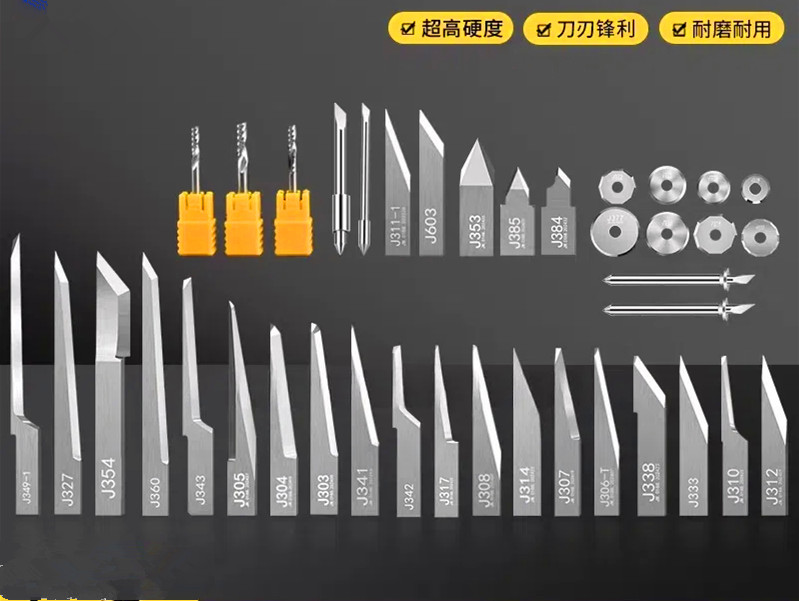
The manufacturing process of tungsten carbide blades (TC Knife Blade) critically impacts their performance by determining hardness, wear resistance, toughness, and cutting precision. Key aspects include:
-
Raw Material Selection and Mixing: High-quality tungsten carbide (WC) powder is mixed with cobalt (Co) powder, which acts as a binder. The cobalt content influences the blade’s strength, hardness, and wear resistance. Precise mixing ensures uniform distribution of particles, which is essential for consistent blade properties.
-
Powder Processing: The mixed powders are crushed, dried, and screened to achieve uniform particle size. This uniformity is crucial for achieving a dense, homogeneous microstructure after sintering, which directly affects blade durability and cutting performance.
-
Pressing and Compaction: The powder mixture is pressed into the desired blade shape under high pressure. This compaction step ensures the particles are tightly packed, which enhances the mechanical strength and toughness of the blade.
-
Sintering: This is the most critical step, where the pressed preform is heated in a controlled atmosphere furnace at high temperatures. Sintering bonds the tungsten carbide particles together and to the cobalt matrix, creating a solid, dense, and homogeneous structure. Precise temperature control and uniform heating during sintering are vital to avoid defects and achieve optimal hardness (Rc 75-80) and wear resistance.
-
Finishing and Grinding: After sintering, blades undergo precision grinding and sharpening to achieve the exact dimensions and a very sharp cutting edge. Advanced grinding technology ensures the blade edge is both sharp and durable, which is essential for efficient cutting and long service life.
-
Quality Control: Rigorous inspections, including ultrasonic flaw detection and dimensional accuracy checks, ensure that blades meet strict quality standards. This prevents premature failures and guarantees consistent cutting performance.
-
Material Properties Resulting from the Process: The combination of tungsten carbide and cobalt, processed through these steps, results in blades with extremely high hardness, excellent wear resistance, and good heat and corrosion resistance. These properties allow the blades to maintain sharpness and cutting efficiency even at high temperatures (up to 500–1000°C) and in harsh environments.
-
Trade-offs: While the process produces very hard and wear-resistant blades, tungsten carbide blades (TC Knife Blade) are more brittle than steel and can chip if subjected to impact or lateral forces. The manufacturing process aims to optimize toughness to mitigate this brittleness without compromising hardness.
In summary, the meticulous manufacturing process—from powder mixing to sintering and finishing—directly determines the tungsten carbide blade’s hardness, toughness, wear resistance, and cutting precision. Advanced technology and strict quality control during these stages ensure blades deliver long life, efficient cutting, and reliability in demanding industrial applications.
Shenzhen Oyea Machinery Co., Ltd. Specialized in manufacturing the following blades:
Zund / Wild
Esko / Kongsberg
Martor
Aristo
Axyz
Bullmer
Summa
EcoCam
iEcho
Atom
Elcede
Sinajet
Stepcraft
Elitron
Comelz
MultiCam
JWEI
Colex
etc.
PREV : Esko Kongsberg Aristo Summa EcoCam Stepcraft MultiCam Oscillating Tangential Knife OTK NEXT : MultiCam 84-00193-BT-562090 AXYZ B2031L-90 double- edged Round Shank Knife Blade